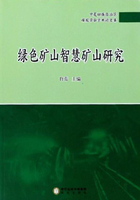
废弃石油井对煤矿采掘活动的危害及治理技术研究
靳 华 马兴华 张 刚 彦 鹏 盛 林
(神华宁夏煤业集团双马煤矿,宁夏灵武750408)
摘要 文章以双马煤矿Ⅰ0104105综采工作面过马探31废弃石油井为背景,讨论了废弃石油井给采掘活动造成的影响及应对措施。通过对石油井结构的分析,确定石油井可能给煤矿采掘活动带来水灾害、油气灾害和顶板灾害;分析了各种灾害的成因及危害后果,提出了井上下综合治理措施以及防治效果。
关键词 废弃石油井 采掘活动 有害气体 危害
由于国内外煤油气共存矿区较少,由此产生的灾害及治理措施不多。石油井的存在不仅给矿区的设计开采带来了困难及资源浪费,而且煤矿开采时具有重大安全隐患,煤矿在采掘过程中一旦揭露油气井,容易造成不可预测的安全事故发生。双马煤矿井田内部的油气井严重制约着煤矿安全高效生产,为降低石油井对井下采掘活动的威胁,有必要进行详细的调研与工程实践,为后续的灾害防治提供翔实的基础资料。
1概 况
双马煤矿位于宁夏回族自治区灵武市东南约60 km处,行政区划分属灵武市和吴忠市盐池县管辖。其中,井田北部属灵武市马家滩镇,南部归属盐池县冯记沟乡。马家滩矿区含油地层和含煤地层是同一套地层,该地区含油地层主要分布在三叠系延长组和侏罗纪延安组,所有油井套管贯穿整个煤系地层。井田内不但有煤炭资源,而且还赋存有丰富的油气资源。石油系统自1953年起先后对陕甘宁盆地的“灵盐定”地区进行了石油普查工作,造成井田内有长庆石油公司的生产油井、废弃石油井、注水井等各类油气井。这些油井遍布在矿区的各个区域,由于施工年代久远、缺乏资料导致部分废弃石油井甚至无法判断在地面的具体位置。根据双马煤矿井田范围内的地质、石油钻孔实际分布情况。2011年至今,针对双马煤矿井田范围内的石油钻孔进行了调查,最终将双马煤矿井田范围内石油井锁定为170个。其中,正在抽采的石油井为1个,废弃石油井为169个,马探31石油井为首次需要治理的废弃石油井。
马探31石油井位于Ⅰ0104105工作面内,其南距Ⅰ0104105工作面开切眼377.09 m,西距Ⅰ0104105工作面回风顺槽75.95 m,东距Ⅰ0104105工作面运输顺槽203.25 m,在工作面119#支架处通过石油井。由于该废弃石油井完井报告已丢失,参考同区域石油井完井资料分析该井井斜为2.4°,马探31石油井地面距4-1煤顶板垂深226 m。据此计算,马探31石油井在井下揭露区域内位置偏差为9.47 m,如图1所示。
图1马探31石油井平面位置
2石油井结构
2.1石油井分类
石油井按钻井目的分为勘探井和生产井,勘探井是以获取地质资料为目的而钻的井,包括地质井、预探井、详探井、评价井等。根据前期工作,认为在双马矿区范围内的油井有勘探井、生产井,并且都为垂直井。
2.2石油井结构特征
一般正常压力系统的井有3层套管:导管、表层套管和生产套管。异常压力系统的井,至少多下一层技术套管。导管的作用是在钻表层井眼时将钻井液从地表引导到钻井装置平面上来,这一层管柱在坚硬地层10~20 m,在沼泽地区可能上百米。表层套管深度一般30~1500 m,通常引导水泥浆返至地表,用来防止潜水层污染,封隔浅层流沙、砾石层及浅层气,也是井口设备(套管头及采油树)的唯一支撑,以及悬挂依次下入的各层套管(包括采油管柱)的载荷。技术套管是钻井期间用来隔离坍塌地层及高压水层,防止井径扩大,减少阻卡机键槽的发生,而且用来分隔不同的压力层系,以便建立正常的钻井液循环,对油层套管起保护作用。生产套管的主要作用是将储集层中的油气从套管中采出来,并用来保护井壁,隔开各层的流体,通常水泥返至产层顶部200 m以上。大多数的套管是用套管接箍连接组成套管柱,套管柱用于封固井壁的裸露岩石。
根据已掌握资料显示,双马井田的油井只有一层生产套管(可能原因是油井的深度较小),井口表面都有表层封井水泥,套管的底部和岩石的缝隙之间都有固定套管的固结水泥,套管内部是否有封井水泥需要进行经验证,如图2所示。
图2双马矿区普通石油井结构
3石油井对采掘活动的危害
由调研和排查结果并根据油井结构中套管和水泥的存在情况,将可能存在的灾害分为:水灾害、油气灾害和顶板灾害三类。水灾害是开采煤层上方的含水层通过油井套管或者油井套管和岩层中间的缝隙溃入工作面。油气灾害分2种情况:①套管和井底油气层导通导致油气涌入工作面,导致人员伤害;②含煤地层本身赋存的油气涌入工作面,导致人员伤害。顶板灾害指的是套管的“超级锚固作用”导致工作面顶板大面积悬顶,并在某个时段垮落产生暴风,导致人员伤害。
3.1水灾害成因及危害
石油井形成了空洞,空洞与含水层连接,如果空洞没有用水泥等材料封堵,就将形成水积累和溃水通道。由空洞形成的情况,可分成如图3所示的3种情况。
图3水灾害示意图
废弃石油井将套管撤走,形成了如图3(1)所示的情况,孔内的水在工作面推进到石油井处,将会按图所示的情况溃入工作面。由于孔内的水量并不大,但水头高度大,可能在揭露过程中产生高压水,需要在制订措施过程中谨慎对待。
废弃石油井或探井没有将套管撤走,并进行了封井工作,形成了如图3(2)中所示的情况。套管和岩层之间的缝隙将形成积水和溃水通道,危害与第一种情况相似,不同之处是水量更小。
废弃石油井或探井没有将套管撤走,也没有进行封井工作,则形成图3(3)中的情况,在处理石油井过程中有2次溃水的可能,需要严加注意。
水灾害是石油井对矿井造成的危害之一,危害性仅次于油气灾害,因此水灾害是灾害治理的主要内容之一。
双马煤矿缓坡副斜井在掘进过程中揭露马浅20废弃石油井,经过现场观测石油钻孔孔径为Φ216 mm左右,在掘进过程中迎头断面施工炮眼时,通过钻杆揭露,当含有油渍的稀泥从炮眼钻孔内流出,流量为1.5~2 m3,掘进揭露油井时流出含有油渍的稀泥为5~6 m3,从开始揭露到过油井共流出稀泥8 m3左右。炮眼孔刚揭露油井时有压力,稀泥为喷射流出,喷射距离为1.5 m,随之压力逐渐减小。同时,缓坡副斜井和主斜井掘进过程中,在6~10煤层之间中下部的细砂岩和粉砂岩层渗出大量石油,根据调查距离最近的马浅20钻孔110 m左右,分析认为马浅20石油通过细砂岩和粉砂岩层的裂隙渗透过来,证明原油渗透力强,且有一定的压力。
3.2油气灾害成因及危害
油气灾害形成必须有通道,根据分析形成了图4所示的2种情况。
图4油气灾害
在无套管和封井水泥的情况下,油气可能已经充满石油井形成的空洞中。当工作面推进到此处进行处理时,油、气可能涌入工作面。根据调研油气中存在甲烷、乙烷、丁烷、戊烷、二氧化碳、一氧化碳、硫化氢等有害气体,需要在揭露过程中对不同气体进行防治,同时空洞内油气压力未知,不能杜绝气体瞬间大量涌入的可能性,如图4(a)所示。
在有套管无封井水泥情况下,油气可能涌入工作面,危害与图4(a)中叙述相同,如图4(b)所示。
油气灾害是废弃石油井造成的最主要危害,危害性大,因此油气灾害作为本次石油井治理的主要任务。
Ⅰ0104105工作面回风顺槽、运输顺槽在掘进、采煤期间出现不同程度硫化氢超限,最高浓度达到350 ppm。同时,在工作面推进80 m后上隅角出现瓦斯超限,最高浓度达到1.13%,通过掘进期间和采煤期间H2S、瓦斯出现位置和浓度变化情况,同时根据长期跟踪测定提出“半径300 m逸散圈”,即以废弃石油井为圆心,油井内H2S等有害气体扩散半径为300 m,见表1。
表1马探31废弃石油井附近煤体内蕴含气体成分分析表
有害气体危害主要表现在:工作面掘进期间及回采过程中,H2S气体大量涌出,浓度严重超出安全限制,严重威胁人身健康,现场作业人员产生眼睛红肿、咽喉干燥、缺氧等不适症状。同时,由于H2S是一种酸性气体,易溶于水生成弱酸类物质氢硫酸,在井下潮湿的空气条件下,对机械设备的腐蚀十分严重,主要表现为液压支架立柱表面镀膜层锈斑、金属焊接点腐蚀脱落等,加速了金属的锈蚀速度,机械设备故障率增加。
3.3顶板灾害成因及危害
顶板灾害分2种情况:①指有套管的废弃油井和探井在地层中起到了“超级锚杆”或锚索的作用,将对其附近的地层产生加固作用,可能导致附近的顶板不能垮落,从而形成大面积悬顶,到一定时候一次性大范围垮落,将采空区的有毒有害气体逼入工作面或者产生暴风,对工作面设备和人员进行损害;②指的是井壁坍塌或者浅部泥沙充填井筒,井筒中含有水、气、油,在工作面通过时,如果不进行处理,可能溃入工作面,导致灾害。
顶板灾害虽然不及油气灾害与水灾害危害性大,但对于局部地层的锚固作用不可忽视,也是此次石油井危害治理的主要任务之一。
4治理措施
马探31石油井无相关完井及封堵资料,综合考虑确定治理方案为:先井上处理,再进行井下处理。井上处理包括透孔、洗井、测井、井筒封堵、加压验封、井口封堵、井场恢复等施工技术措施。井下处理包括从已有巷道掘进至油井附近、打探眼确定油井位置、切割油井套管、若有通道进行封堵等进行油井治理。
4.1地面治理工艺
根据马探31石油井实际情况,采用全井筒水泥浆封孔方法,通过透孔、水泥封堵、加压验封等工程措施,完成治理任务。工艺流程如图5所示。
图5施工工艺流程
4.1.1透孔
透孔主要是清除Φ140 mm生产套管内杂物,检查套管是否变形、井深是否合格。本次透孔采用回转钻进方法,稀泥浆钻进。钻具组合:Φ60 mm钻杆+Φ68 mm钻铤+Φ114 mm钻头。
4.1.2气体取样及防护
井场50 m内严禁烟火,做好防油气着火、防有毒有害气体中毒、防井喷工作,在透孔过程中如果发现有毒气体逸出,应对气体取样,明确气体成分。
4.1.3制作人工井底
透孔至700 m后,如果700 m以下未封固,则在700 m处制作人工井底,为水泥浆封堵做好准备工作。
4.1.4水泥浆封堵
全井筒注入密度≥1.82 kg/L油井水泥浆,水泥浆高度距井口15~20 m时,停止注浆、候凝,封堵如图6所示。
图6马探31石油井封孔
4.1.5加压验封
水泥浆在井筒内候凝72 h后,安装好井口,用水泥车试压,验证封堵效果,施压15 MPa,30 min内压力下降不超过0.5 MPa为合格,如果压力下降超过0.5 MPa,注入低黏度高强度凝胶封堵材料,候凝24 h后,重新验压,直到压力不降为止。
透孔过程中,在钻进至9.5 m~49 m井段、200 m~248 m井段、400 m~430 m井段过程中,漏失严重,采取了增加膨土剂、调整泥浆密度措施,保证了透孔工作顺利完成;根据透孔情况,调整了封堵措施,不做人工井底,直接采取全孔段水泥浆封堵,加快封堵进度;矿方全程安排专职人员跟班,进行协调,同时对封堵过程进行质量监督,达到了封堵设计要求,顺利完成了地面封堵工作。
4.2井下治理工艺
为确保工作面顺利通过马探31石油井,结合地面治理情况,最终确定井下揭露技术方案按照“探查-探眼-揭露-切割-封堵”程序进行,采煤工作面过石油井采用钻孔探查,检查孔内气体浓度、涌水等情况。无异常后,工作面煤壁距石油井最小法向距离15 m位置时,开始施工探眼钻孔,逐步确定石油井的具体位置,然后施工探巷揭露石油井。具体步骤:
(1)工作面煤壁距马探31石油井最小法向距离100 m时,以石油井垂直投影工作面煤壁位置为中心,上下各15 m范围内布置垂直煤壁的超前探查孔,探查孔布置在煤层厚度的中间位置,平行于顶底板施工,探查孔间距为5.0 m,共计7个探查孔,孔深不小于30 m,任何时候,都要保证工作面煤壁前方有不小于20 m的探查孔超前距离,直至工作面距离石油井15 m。
(2)工作面煤壁前方20~30 m,工作面风机两巷倾斜顺层钻孔连续注硫化氢吸收液,降低工作面回采过程硫化氢浓度。
(3)施工探查钻孔过程中,必须有安检员在现场时刻检查钻孔内有无异常状态的气体涌出和异常涌水、渗油等情况,出现异常情况,立即停止作业,人员撤离至运输顺槽新鲜风流中。工作面回采前,必须检查钻孔内有无异常状态的气体涌出和异常涌水、渗油等情况,确认无异常后,工作面方可开始回采。
(4)工作面煤壁距马探31石油井最小法向距离15 m时,以石油井垂直投影工作面煤壁位置为中心上下各10 m范围,布置探眼钻孔,用钻机向煤壁打25 m深钻孔9个,间距2.5 m。
(5)工作面煤壁距马探31石油井最小法向距离10 m时,以石油井垂直投影工作面煤壁位置为中心上下各10 m,布置17个探眼钻孔,用钻机向煤壁打20 m深钻孔,间距1.25 m。
(6)工作面煤壁距马探31石油井最小法向距离5 m时,以石油井垂直投影工作面煤壁位置为中心上下各10 m,布置33个探眼钻孔,用钻机向煤壁打15 m深钻孔,钻孔间距0.625 m;若未找到石油井,则在两钻孔间,增加一个钻孔,按此程序一直循环操作,直至探到石油井为止。在施工探眼钻孔过程中,根据现场钻孔探石油井具体情况,进行相应加密调整,探眼孔间距最小时,可减小到100 mm。钻孔位置始终垂直于煤壁。
(7)如果在钻孔施工过程中,其中有任何一个钻孔探到石油井的位置时,在此钻孔附近局部范围内加密施工间距为300 mm的钻孔,确定石油井的具体位置,采煤机低速运行割煤逐步揭露。
(8)石油井揭露后,采用人工切割石油井套管及抽油管。顶板处油管切割位置要高于煤层顶板200 mm,使用铁板烧焊封盖,以防止顶板以上水、油气涌入工作面;底板处油管切割位置低于底板200 mm,并人工开挖1 m见方的基坑,使用混凝土进行浇筑包裹封堵。
5结束语
(1)通过地面封堵,切断了石油井深部有害气体持续向煤层渗透的补给来源,为工作面瓦斯、H2S等有害气体的防治奠定了基础,为有害气体的防治创造了有利条件。同时,将油井孔内赋存水排出,切断了直罗组砂岩含水层及煤层底部承压含水层向工作面充水的通道和来源,消除了水害威胁。
(2)通过探查工作,验证“先探后采”的必要性,探清石油井附近煤层内有害气体浓度、压力和钻孔水赋存情况,为判断过石油井可能存在的风险提供依据。同时,确定石油井在工作面向西偏移的事实,划定工作面重点防范范围。
(3)通过对石油井封堵前后工作面有害气体的监测比对分析,判定工作面出现的硫化氢、瓦斯气体主要来源于马探31石油井,而且从不同位置、不同时点、不同监测手段采集数据综合分析得出以下结论:从走向上看,距马探31石油井距离越近,煤层瓦斯含量越高;从倾向上看,距马探31石油井距离越近,煤层瓦斯含量越高;H2S、瓦斯出现位置和浓度变化情况,是以马探31石油井为中心,扩散半径为300 m形成气体“逸散圈”,对采掘活动构成威胁。通过采取“注射吸收剂、喷洒吸收液、增加风量、降低割煤速度、加强气体监测、完善个体防护”综合防治硫化氢措施,有效遏制灾害的扩大和升级,取得了良好效果。
参考文献
[1]王金国,李慧平.煤矿井田内废弃油井治理的摸索与实践[J].煤炭技术,2014(4):262-265.
[2]毕胜,徐超.煤矿井下硫化氢气体综合治理体系的探讨[J].煤炭技术,2017(6):126-128.
[3]刘瑞杰.油井硫化氢的治理效果分析[J].油气田环境保护,2017(4):22-24.
[4]刘世峰,袁炳强.石油钻井井身结构及钻机设备的选择[J].石油和化工设备,2010(12):41-42.
[5]张志朋.钻井设备的发展现状及质量控制[J].中国化工贸易,2013(2):41-42.
作者简介
靳华,生于1984年,工程师,2017年毕业于西安科技大学,现任职于神华宁夏煤业集团双马煤矿,主要从事井工煤矿生产技术管理与研究。